The
Last month FireEye released a report detailing an incident that their subsidiary Mandiant responded to at a critical infrastructure organization. Here a malware framework, dubbed TRITON (also referred to as TRISIS or HatMan), was discovered targeting the Schneider Electric Triconex line of industrial safety systems, allegedly in order to cause physical damage and shut down operations. The activity was believed to be consistent with a nation-state preparing for an attack. According to a Dragos report on the same malware, their team discovered TRITON being deployed against at least one victim in the Middle East in mid-November 2017.
This blog post aims to discuss the incident background, the TRITON framework and the attack payload in an effort to clarify this attack in particular and attacks on industrial safety systems in general. It draws upon previously published reports by FireEye, Dragos and ICS-CERT as well as analysis (which can be found here) by Midnight Blue and Ali Abbasi of the publicly available malware. Further details of the incident and malware are likely to be discussed by others during this week’s S4x18 TRITON/TRISIS session.
Summary
TRITON is the first publicly known example of malware targeting industrial safety controllers, an escalation with serious potential consequences compared to previous ICS-focussed incidents. It has been deployed against at least one victim in the Middle East with no indications of victims outside of the Middle East so far. TRITON is a framework for implanting Schneider Electric Triconex safety controllers with a passive backdoor through which attackers can, at a later point in time, inject potentially destructive payloads.
Though the potential impact is very serious (including infrastructural damage and loss of life resulting from sabotaging critical safety systems) it is important to nuance the threat posed by the discovery of this malware, especially when the original attacker intent remains speculative. In addition, the attack is not very scalable even against other Triconex safety controllers due to the complexity of required industrial process comprehension. However, a sufficiently knowledgeable and well-resourced attacker seeking to target a facility using Triconex controllers as part of its safety systems could repurpose TRITON, thereby lowering the bar somewhat by removing the barrier of reverse-engineering the proprietary TriStation protocol. The incident is illustrative of various woes in the industrial cybersecurity world which have been discussed extensively over the past years, ranging from devices which are ‘insecure by design’ and have been exposed to hyper-connected environments they were not quite designed for to a lack of basic IT/OT security hygiene and early warning insights on part of asset owners.
Background
TRITON is one of the few publicly known examples of malware targeting Industrial Control Systems (ICS), after Stuxnet, Havex, Blackenergy2 and
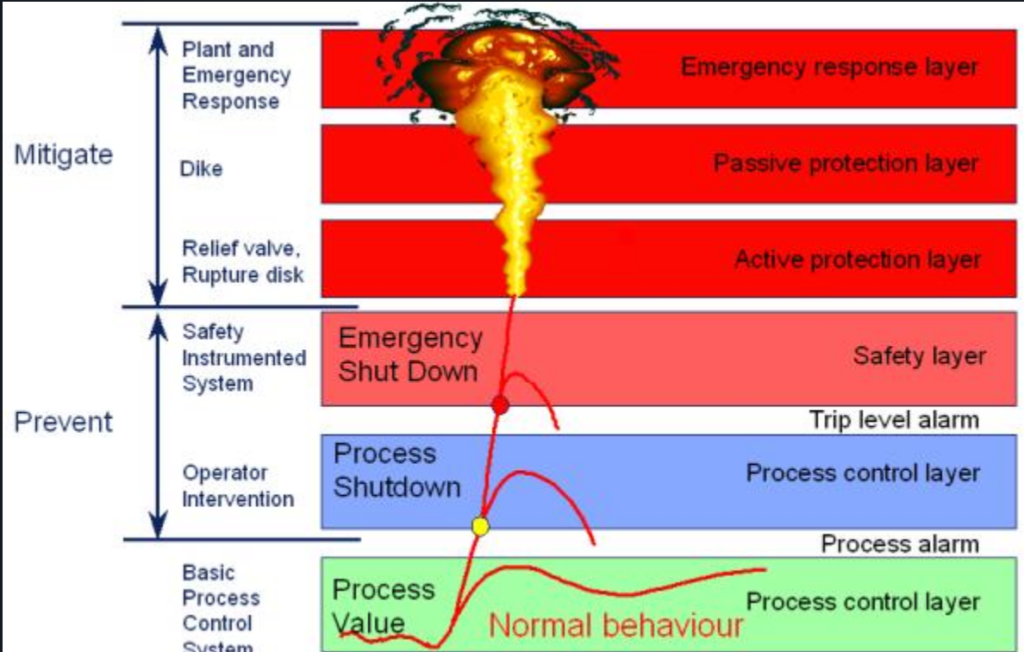
infrastructure organization are typically a kind of Programmable Logic Controller (PLC) designed to high standards with redundant modules and tend to as that allows for safe failure in case the main processor fails or power is lost. They are deployed in a manner specific to the process environment requirements and are usually configured in one of the IEC 61131-3 programming languages (eg. LD, ST, etc.). Of course, safety is
Traditionally, SIS connectivity is limited and systems are segregated from the rest of the Operational Technology (OT) environment which would limit the potential impact of safety controller security issues. But over the years, as part of a broader trend in embedded systems in general, this isolation has made way for more and more connectivity and systems integration. While this integration comes with benefits in terms of cost, usability and process insights for business intelligence purposes, the flip side is that it exposes systems that were never designed for secure connectivity in the first place to the wider OT and IT environments and by extension to whatever the wider network itself is exposed to. The potential implications of a malicious SIS-compromising attacker are serious and could range from shutting down a process to allowing for unsafe states and manipulating other parts of the OT environment to create such a state which might result in financial losses, damage to equipment, products and the environment or human safety and loss of life.
But it’s important to nuance this image and avoid alarmist headlines. First of all because fear, uncertainty and doubt cause sensible analysis and good advice to be lost amid sensationalism and help create a ‘boy who cried wolf’ effect where the stock that ICS equipment vendors and OT asset owners and operators put in the opinions of the security industry as a whole erodes over time. Secondly, while the initial steps along the ‘ICS Kill Chain‘, up to and including the compromise of the safety controller, might seem relatively simple, crafting the ‘OT payload‘ that actually does the damage is typically neither easy nor scalable. As pointed out by Benjamin Green, Marina Krotofil and Ali Abbasi such attacks require a high level of process comprehension which would have to be derived from analysis of acquired documents, diagrams, data historian files, device configurations and network traffic. This would have to be done on a facility-to-facility basis since even attacks against two functionally similar facilities will require attackers to take differences in process scale and design, equipment and device configuration into account.
In the case of SIS that means that a security compromise does not trivially compromise process safety. Apart from the SIS, the facility in question might have safety measures ranging from sacrificial parts in machines, enclosures and blast dampers to alarms and emergency procedures and as such assessing the implications of SIS compromise would require facility-specific process comprehension as well. This does not mean that such worst-case scenarios are infeasible but that the attacker space capable of bringing them about and their scalability are more limited than often portrayed.
The Incident
The FireEye report claims that the attacker gained remote access to a Triconex engineering workstation running Microsoft Windows as well as the Distributed Control System (DCS). The attacker deployed a Py2EXE application, which was disguised as a benign Triconex log reviewing application named Trilog.exe, containing the TRITON framework on the engineering workstation together with two binary payload files named inject.bin and imain.bin. TRITON does not leverage any 0-days but instead reprograms the target safety controllers via the TriStation protocol (discussed below) which lacks authentication (though ACLs could have been configured on the controllers). As the TriStation protocol is proprietary and undocumented this means the attacker had to reverse engineer it, possibly through a combination of using similarities with the documented Triconex System Access Application (TSAA) protocol, inspection of traffic between the engineering workstation and the controller and reverse-engineering of workstation software and controller firmware.
The TRITON framework is capable of autodiscovering Triconex controllers on the network by sending a UDP broadcast message over port 1502 but this functionality was not used during the incident. Instead the IP addresses of the target controllers were specified directly and upon connection the status of the controller was retrieved over TriStation. If the controller was running the inject.bin and imain.bin payload files were injected into the controller program memory and a periodic check was initiated to see if any error was detected. If so, TRITON would reset the controller to the previous state over Tristation and if this failed it would write a dummy program to memory in what was likely an attempt at anti-forensics. During the incident, the industrial process was shutdown as a result of some controllers entering a failed safe state which caused the asset owner to initiate the investigation. The cause of this failed safe state was reportedly a failed validation check between the three separate redundant Triconex processor modules.
The fact that both the DCS and SIS systems were compromised suggests the attacker intended to cause serious damage rather than a mere process shutdown. This hypothesis is strengthened (though not indisputably confirmed) by the fact that the attacker apparently made several attempts to deliver a specific control logic to the safety controllers rather than merely shut them down.
Triconex Safety Instrumented Systems (SIS)
The Schneider Electric Triconex line of safety controllers consists of the Tricon (CX), Trident and Tri-GP systems all of which share the triple modular redundancy (TMR) architecture. While the incident targeted Tricon 3008 controllers specifically, the heart of the attack is the (ab)use of the unauthenticated TriStation protocol and as such all safety controllers running this protocol are potentially affected.
The Schneider Electric Triconex line of safety controllers consists of the Tricon (CX), Trident and Tri-GP systems all of which share the triple modular redundancy (TMR) architecture. While the incident targeted Tricon 3008 controllers specifically, the heart of the attack is the (ab)use of
Read the remaining article at https://www.midnightbluelabs.com/blog/2018/1/16/analyzing-the-triton-industrial-malware